Understanding Welding WPS Specifications: Finest Practices and Techniques for Top Quality Welds
In the world of welding, understanding Welding Procedure Specification (WPS) requirements is a vital element that directly influences the top quality and stability of welds. Complying with these standards makes sure uniformity and dependability in welding results. Nevertheless, attaining excellence in welds goes beyond just comprehending the criteria; it involves executing finest practices and techniques that boost the craft to a level of accuracy and ability that establishes apart the standard from the outstanding. As we navigate through the complexities of welding WPS standards, revealing crucial understandings and strategies for attaining top-tier welds will be extremely important for welders looking for to master their craft and create welds that stand the test of time.
Recognizing Welding WPS Specifications
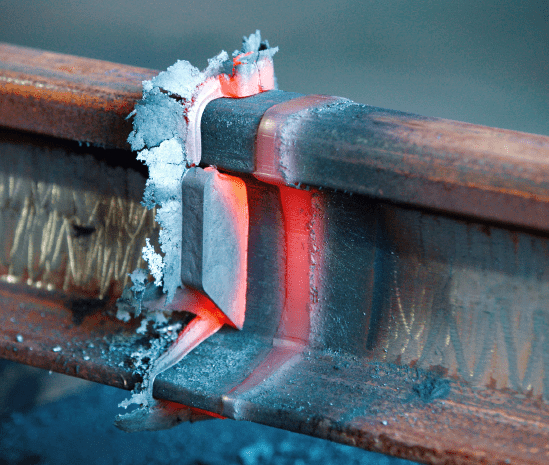
Assessors depend on WPS documents to validate that welding treatments are being followed appropriately and that the resulting welds are of high quality. Engineers use WPS criteria to design welding treatments that make certain the resilience and reliability of welded structures.
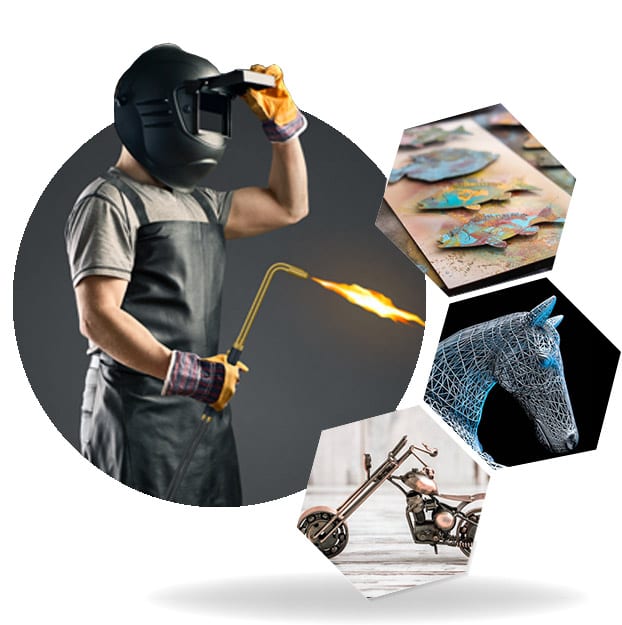

Necessary Tools for High Quality Welds
Understanding welding WPS criteria is important for welders to efficiently utilize the necessary devices required for producing top quality welds. One of the most critical devices for high quality welds is a welding equipment. The kind of welding machine required depends upon the welding process being made use of, such as MIG, TIG, or stick welding. Welding headgears are additionally indispensable to secure the welder's eyes and face from stimulates, warmth, and UV radiation. In addition, welding handwear covers constructed from long lasting and heat-resistant products safeguard the hands from injuries and burns. Clamps and magnets aid hold the work surfaces with each other firmly throughout the welding process, ensuring accurate and accurate welds. Cord brushes and chipping hammers are important for cleaning up the weld joint before and after welding to get rid of click site any impurities that could impact the high quality of the weld. Finally, a measuring tape and angle mill are helpful tools for making certain correct placement and preparing the workpieces for welding.
Key Techniques for Welding Success
To accomplish welding success, one need to understand the essential methods vital Resources for creating top quality welds. Maintaining a secure welding and a consistent hand setting throughout the process is essential to accomplishing accuracy and uniformity in the welds. By mastering these essential techniques, welders can raise the top quality of their job and accomplish welding success.
Ensuring Compliance With WPS Criteria
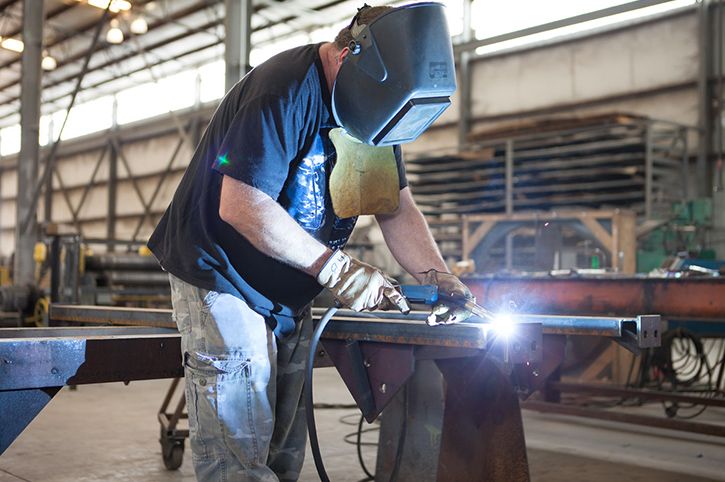
Additionally, welders should go through training to acquaint themselves with the WPS standards pertinent to their job. Routine audits and inspections must be conducted to confirm that welding tasks line up with the recommended WPS standards. Additionally, preserving thorough documents of welding parameters, equipment calibration, and inspection results is crucial for showing conformity with WPS requirements - welding WPS. By carefully adhering to WPS standards, welders can make certain that their job fulfills the required top quality levels and adds to the overall success of the welding job.
Troubleshooting Common Welding Issues
To resolve click reference this, making sure proper cleaning of the base steel prior to welding and utilizing the appropriate shielding gas can substantially decrease porosity. In addition, distortion, cracking, and spatter are common welding challenges that can be alleviated via correct joint prep work, consistent warmth control, and choosing the suitable welding consumables. By extensively comprehending these typical welding problems and their origin triggers, welders can successfully repair problems and achieve high-grade welds.
Final Thought
To conclude, understanding welding WPS requirements requires a detailed understanding of the guidelines, making use of important tools, and carrying out key techniques for successful welds. Making sure compliance with WPS standards is vital for creating top quality welds and staying clear of typical welding problems. By following best practices and strategies, welders can attain consistent and reputable lead to their welding jobs.
In the world of welding, understanding Welding Treatment Specification (WPS) standards is a vital part that directly influences the top quality and integrity of welds.When diving right into the realm of welding practices, a vital aspect to comprehend is the significance and details of Welding Procedure Requirements (WPS) requirements. WPS requirements offer a detailed guideline for welding procedures, making certain uniformity, top quality, and safety and security in the welding process. The type of welding maker required depends on the welding procedure being made use of, such as MIG, TIG, or stick welding.Achieving welding success through the proficiency of crucial techniques demands a thorough understanding and adherence to Welding Treatment Spec (WPS) criteria.